Когато беше представен новият Audi E-Tron GT, местоположението на Audi Sport Bôllinger Höfe в Heilbronn, Германия, бързо се нуждаеше от почти 200 нови инструмента и приспособления за неговото производство. Проектирането на тези инструменти струва много време. И аутсорсването на производството понякога може да отнеме много седмици до месеци. Това е мястото, където автоматизацията на дизайна и 3D печатът предоставиха несравним работен процес за Audi Sport.
Фабриката на Audi Sport Böllinger Höfe е съоръжение за производство на автомобили от висок клас. Техният основен производствен фокус е върху Audi R8 и напълно електрическото Audi E-Tron GT. Тези автомобили са “крем дьо ла крем” от реномирания немски автомобилен производител. На поточната линия е изписана немска ефективност. Голите клетки идват на роботизирани платформи и се монтират на горна релса. След това този влак от ексклузивни автомобили преминава през много гари, където се монтират специфични за поръчката части. Трудно е да забележите два еднакви автомобила един до друг, което прави цялата операция още по-впечатляваща.
Всяка станция има ограничено време за сглобяване на части и монтирането им на автомобила. Ето защо оптимизираният и ефективен работен процес е от решаващо значение за механиците. Специализираните инструменти и приспособления играят огромна роля, за да направят работата на механиците много по-бърза, лесна и ергономична.
„Ние произвеждаме близо осемстотин инструменти и приспособления за нашата фабрика тук“, каза Cem Guelaylar, експерт по 3D печат в Audi Sport. „Аутсорсингът се нуждае от повече от две или три, четири седмици или месеци. Зависи от доставчика и процеса за доставяне на поръчката до доставчика. 3D принтирането ни помогна да получим тези инструменти за много кратко време. Идват при нас работниците и казват, трябва ми “арматура за сглобяване на колите”. Отнема един ден, за да вземе този инструмент в ръката си.
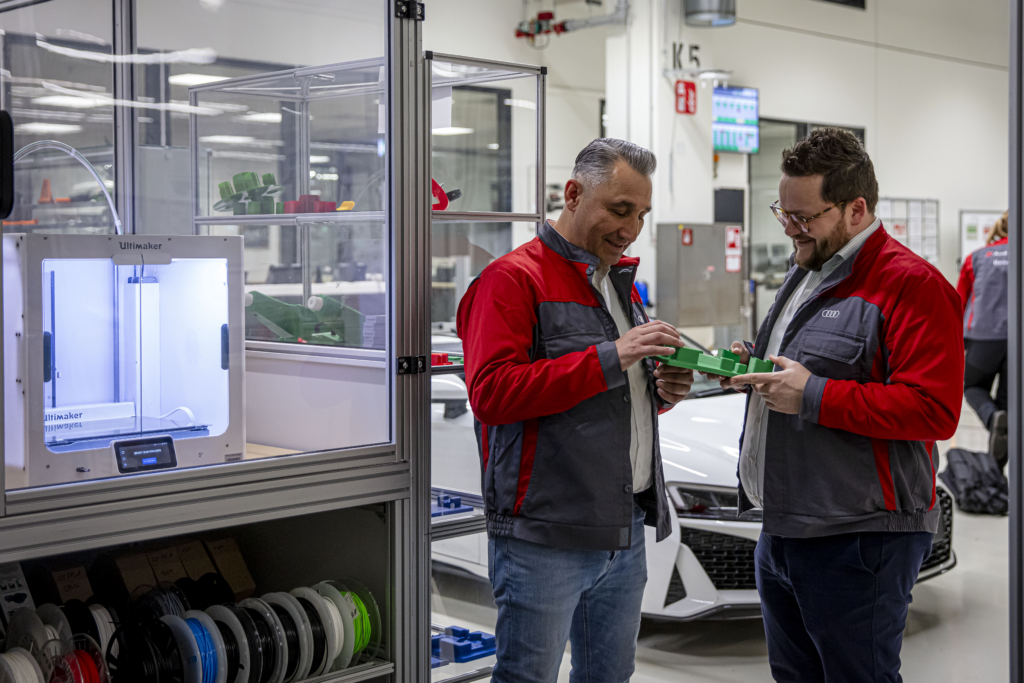
Различни инструменти за различни приложения
Има персонализирани инструменти, които помагат за подравняването на частите по време на монтажа. Например за монтиране на покрив или лога от външната страна на автомобила. Това повишава последователността и качеството на крайните автомобили, като същевременно спестява минути на автомобил. Инструментите за контрол на качеството гарантират, че всички автомобили отговарят на най-високите стандарти на Audi. Тези персонализирани приспособления се монтират към части на автомобила за измерване на подравняването и допуските. Например, Audi Sport създаде персонализирана приставка за фокусиране на Head Up дисплея (HUD) върху арматурното табло на автомобила. Приспособлението използва два лазера, които се проектират върху инсталирания HUD. Когато лазерите се подравнят, това означава, че отразяващото стъкло е монтирано правилно.
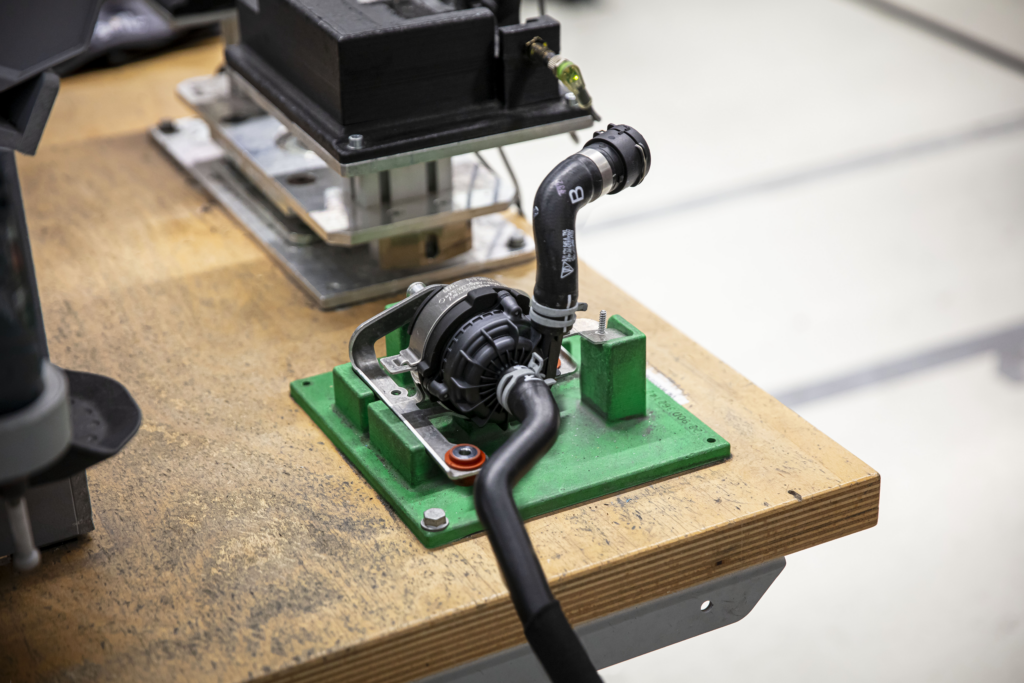
Много части трябва да бъдат сглобени, преди да бъдат монтирани на автомобилите. Тръби, добавени към централна плоча за флуиди, кабели и радиатори към централен контролен блок, списъкът може да продължи. Работата върху тези части, просто положени върху работното бюро, прави задачата много трудна. Това е мястото, където Audi Sport използва много приспособления в своята фабрика. Тези приспособления държат частите на място за лесно и бързо сглобяване. Тези приспособления не само спестяват часове, но и оказват голямо влияние върху последователността на производството. Много от тези приспособления също са проектирани да имат положително въздействие върху ергономията на работника. Например като държите инструментите в по-добра посока за работа.
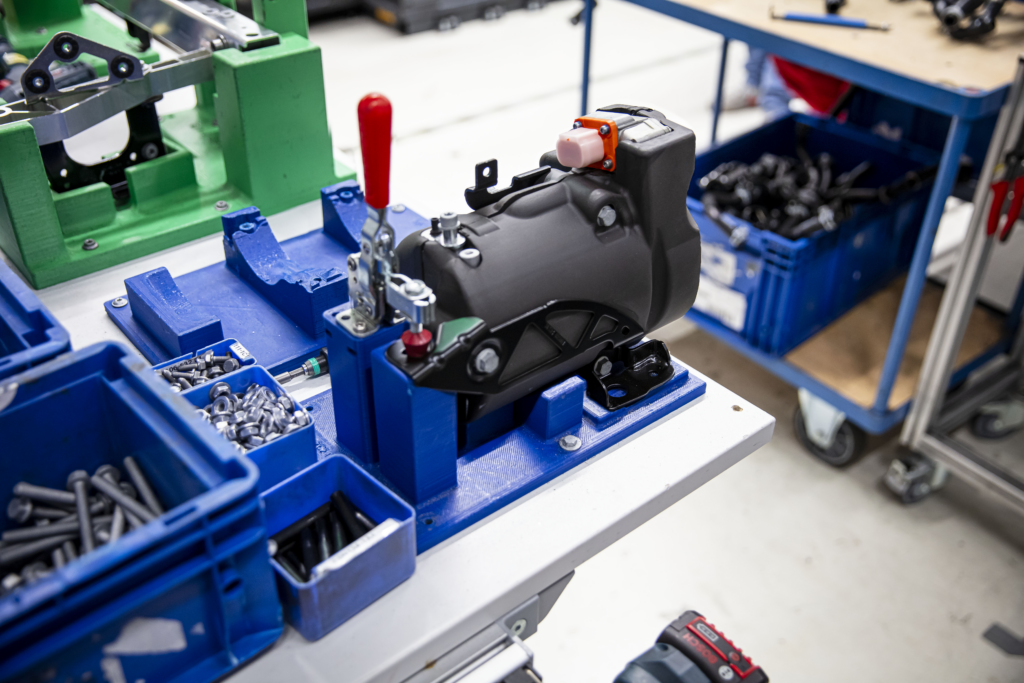
Проектиране на части за минути вместо часове
Така че, когато беше представен новият E-Tron GT, възникна голямо предизвикателство да се създадат близо 200 различни инструмента и приспособления. И имаха нужда от тях бързо, за да започнат производството. Проектирането на тези инструменти струва много време и опит. Те трябва да бъдат точни, лесни за употреба и лесни за производство. Тук съотборникът на trinkle изигра голяма роля. Fixturemate е софтуер, специално създаден за създаване на приспособления за сглобяване. Част се внася и поставя под прав ъгъл. След това приспособлението се създава чрез добавяне на основна плоча, места, където частта се нуждае от опори и отвори, за да може да се монтира към бюро. Има и библиотека от готови инструменти, като например скоби. Софтуерът е достатъчно лесен за използване, така че всеки може да го използва. И докато проектирането на инструменти може да отнеме часове в традиционния CAD софтуер, то се нуждае само от 10-20 минути във fixturemate.
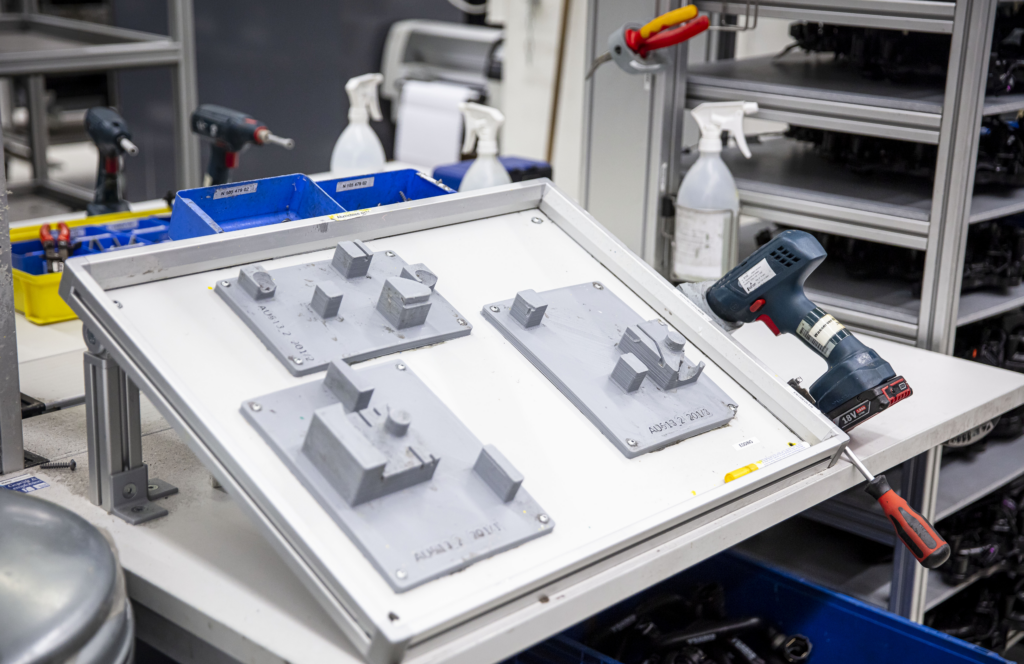
„Започнахме да произвеждаме напълно електрическия автомобил Audi E Tron GT тук. Имахме нужда от почти двеста приспособления и инструменти за тази нова кола. Fixturemate ни помогна за кратко време да донесем много приспособления“, отбеляза Guelaylar . „Поставяме нашите части във Fixturemate, изваждаме устройството от този софтуер за минути. Обикновено при класическото строителство ни трябват два часа, три часа, четири часа, в зависимост от размера на детайла. Fixturemate е много лесен за използване. Можем да доведем стажанти и да им покажем как да използват софтуера fixturemate и те могат директно да работят с този софтуер и да донесат графиката за кратко време.“
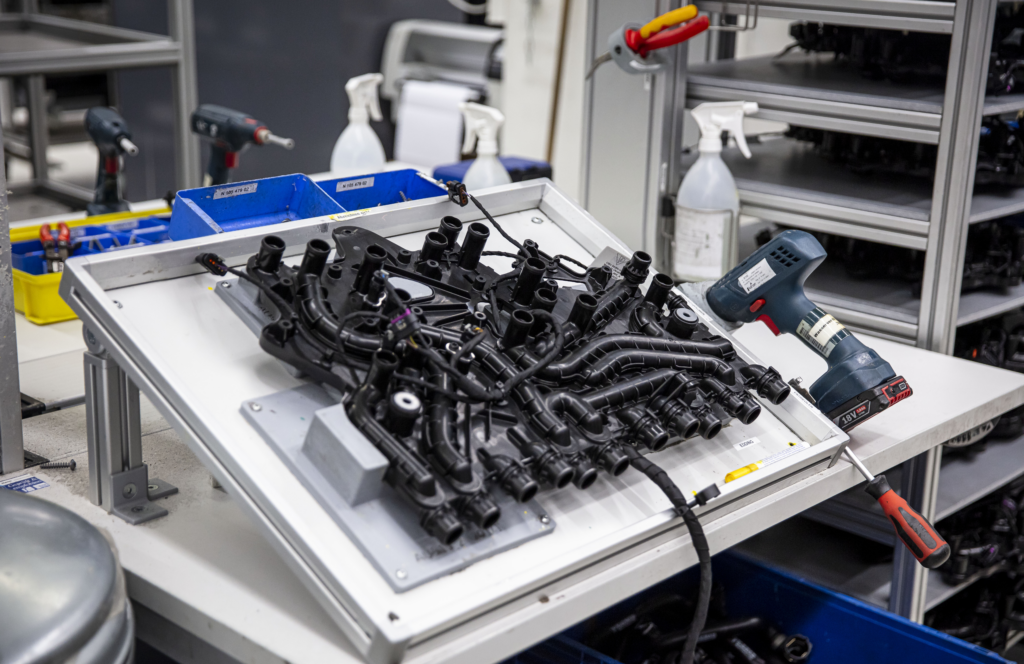
Предимствата на 3D принтирането в Audi Sport
Audi Sport не само имаше нужда частите да бъдат проектирани бързо, но също така трябваше да бъдат произведени за много кратко време. Възлагането на производство на инструменти на външни изпълнители е скъпо и може да отнеме много седмици до месеци. Ето защо Audi започна със стая за 3D печат. Няколко принтера като Ultimaker S5 позволяват на Audi Sport да произвежда техните нужди от инструменти. Инструментите вече могат да бъдат отпечатани за един ден на малка част от цената. Няма нужда да изисквате оферти, да инструктирате доставчици и да чакате части да бъдат произведени и доставени. Когато дадена част не отговаря на изискванията, тя може директно да бъде подобрена и препечатана.
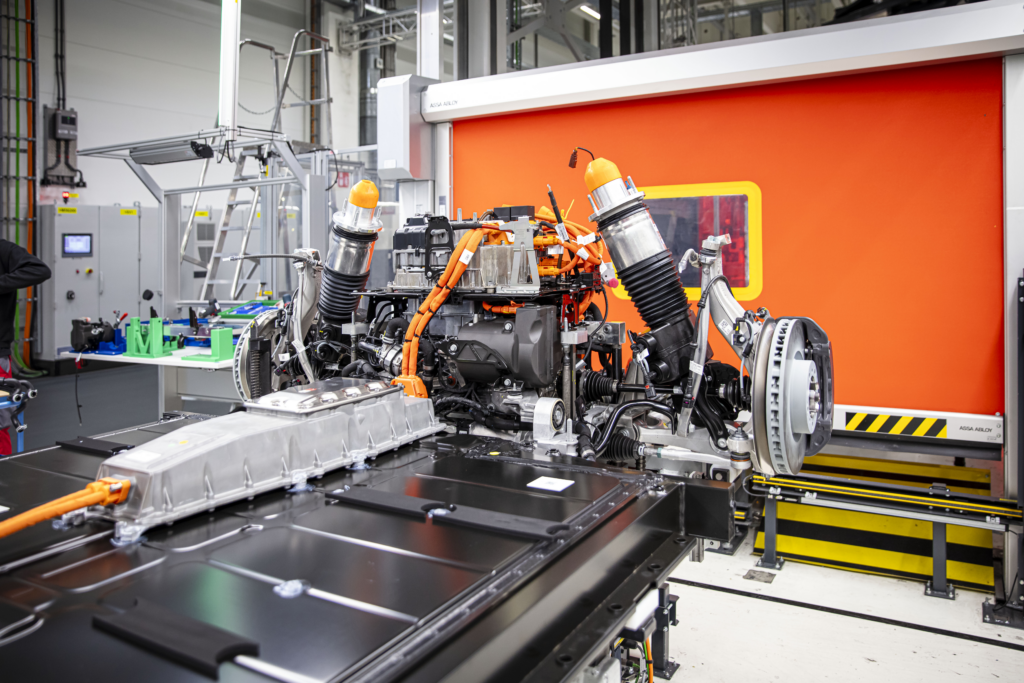
Правилният материал за работата
Повечето от приспособленията са отпечатани с Tough PLA. Този материал има подобни свойства на гъвкавост и здравина като ABS, но печата много лесно без предизвикателствата на ABS. Има и отпечатани инструменти за защита на автомобилни части с помощта на TPU95a. Мекият материал е идеален за предотвратяване на повреда на части.
Благодарение на екосистемата на UltiMaker, Audi Sport също има достъп до стотици материали на трети страни. Тези материали често имат много специфични свойства. Един от тези материали, които Audi Sport използва, е безопасен срещу ESD PLA, който се използва за приспособления, които работят с електронни компоненти. Подготовката на 3D разпечатки с тези материали става без усилие с помощта на Ultimaker Cura, тъй като профилите за печат са достъпни безплатно на пазара.
„Използваме Tough PLA, защото е евтин и лесен за използване. Ние използваме TPU най-вече за защита и за защита на автомобилни части. Ние също така използваме ESD безопасни материали и понякога ABS или PETG. За нас 3D принтирането е много бързо и полезно нещо за нашата фабрика и нашите работници,” продължи Guelayler.
Audi Sport наистина се отличава с постоянно намиране на повече ефективност. Като започнаха 3D печат за своите инструменти, те намалиха разходите за производство на инструменти с над 80%, като същевременно доставят тези инструменти на работниците за един ден вместо за няколко седмици. На всичкото отгоре, с помощта на fixturemate, Audi Sport направи дизайна на приспособления лесен и бърз. Не се нуждаете от специален CAD-дизайнер, за да създавате дизайни на тела. От проектиране до 3D печат, всеки може да създаде необходимите инструменти и да започне да се възползва.
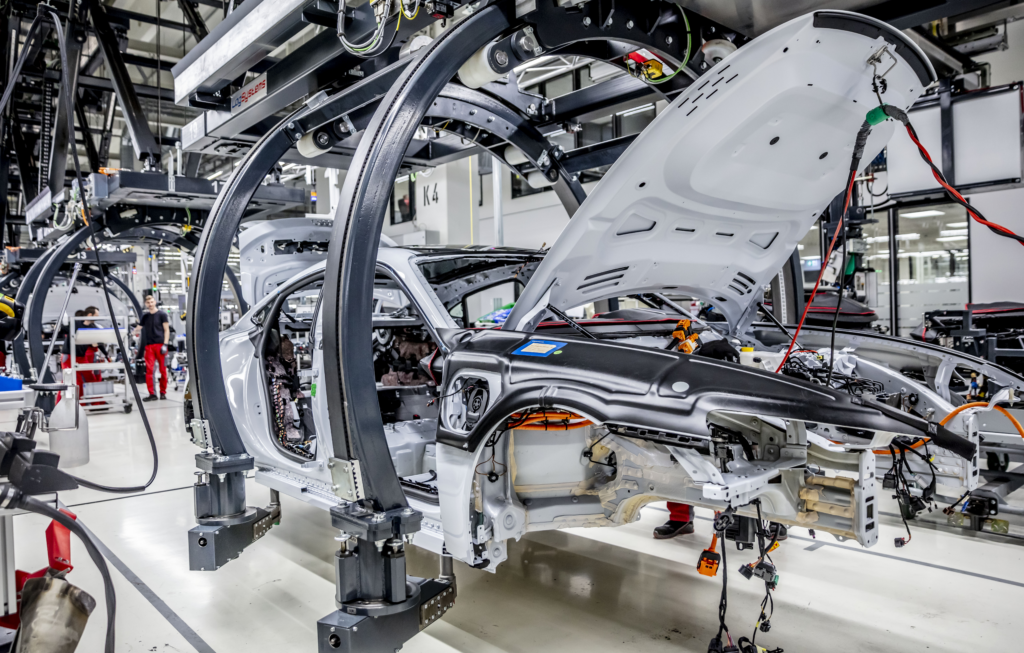
Вижте видеото, което Audi Sport сподели за темата:
А на линка по-долу можете да получите консултация и да си поръчате UltiMaker S5, и други продукти на UltiMaker, да получите обучение, сервизна и извън сервизна поддръжка: