Ford Motor Company е използвала SLA и SLS 3D принтери от Formlabs, за да създаде прототип на няколко компонента за своя нов SUV Electric Explorer.
Шестият по големина производител на автомобили в света, Ford тества бета най-новия 3D принтер на Formlabs, Form 4 , за да рационализира своя процес на проектиране на автомобили. Това се добавя към съществуващите системи Formlabs Form 3L и Fuse 1+ 30W .
Компанията използва 3D печат за прототипиране на дизайни за ключови компоненти на своя нов електрически SUV, включително огледала, дръжки, портове за зареждане и части на таблото. Съобщава се, че това е позволило на екипа на работилницата да поема повече рискове, да отключва сложни дизайни и бързо да създава прототипи на нови дизайнерски итерации за часове, а не за дни.
Чрез рационализиране на своя процес на проектиране с адитивно производство, Ford се надява да изпълни ангажимента си да предложи гама изцяло електрически превозни средства (EV) в Европа до 2030 г. Съобщава се, че скоростта на 3D печата е от съществено значение за спазването на този кратък срок.
„Ако нямахме достъп до адитивно производство, нямаше да можем да се конкурираме с конкурентите, нямаше да можем да бъдем толкова бързи“, обясни Bruno Alves, експерт по адитивно производство и специалист по инструменти във Ford.
„Производството на добавки е много важно в процеса на развитие. Това ви дава възможност да произвеждате части много бързо, много ефективно и да намалите разходите,” добави Sandro Piroddi, ръководител на Rapid Technology Center във Ford.
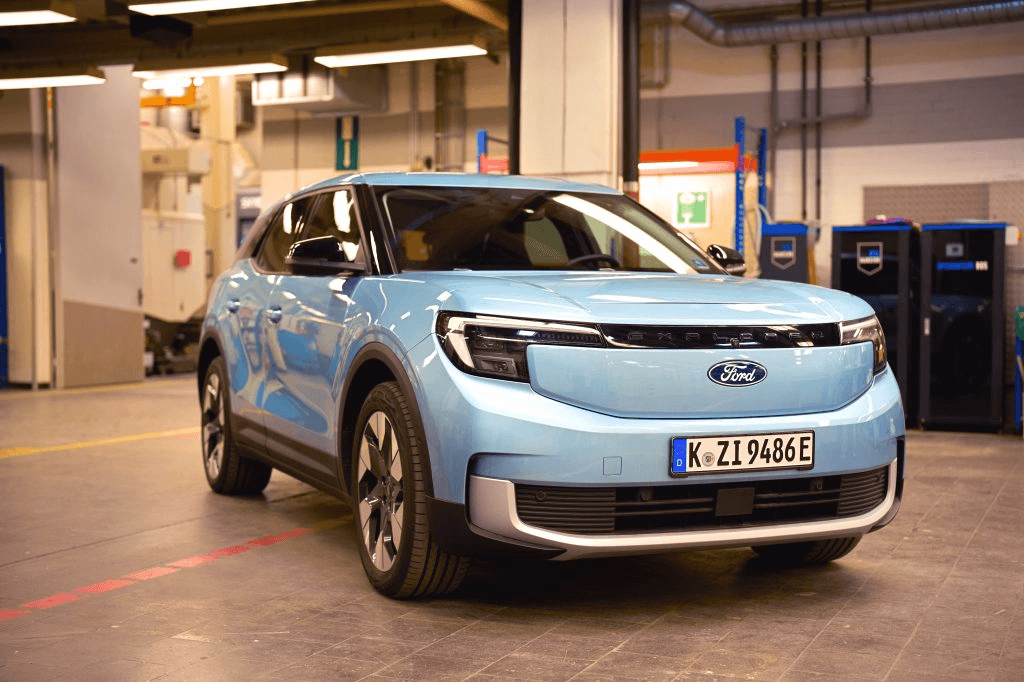
Новият Ford Electric Explorer. ( Снимка чрез Ford Motor Company.)
Ford използва новата Form 4 на Formlabs
Центърът за бързи технологии PD Merkenich на Ford е развойната база на автомобилния производител, отговорна за проектирането на всички пътнически превозни средства за европейския пазар. Тук SLS, SLA, FDM и металните 3D принтери отдавна играят роля в производството на прототипи на превозни средства.
Трябва да се отбележи, че 3D принтерите със смола от Formlabs играят ключова роля в проектирането на най-новата гама електромобили на Ford, включително SUV Electric Explorer. SLA 3D принтерите се използват главно в работилници за проектиране на прототипи, които изискват висококачествено покритие на повърхността. Тези части също трябва да бъдат произведени бързо, за да позволят бързи итерации.
Ford стана една от първите компании, които приеха Form 4, най-новия MSLA 3D принтер на Formlabs.
Пуснат по-рано тази година, Form 4 предлага високоскоростен 3D печат, надеждност и качествени свойства на материала. Неговите ускорени скорости на печат са значителна разлика от неговия предшественик, Form 3+ . Новият полимерен 3D принтер може да изпълнява стандартни задания за печат за по-малко от два часа и може да се похвали с вертикални скорости до 100 мм/час.
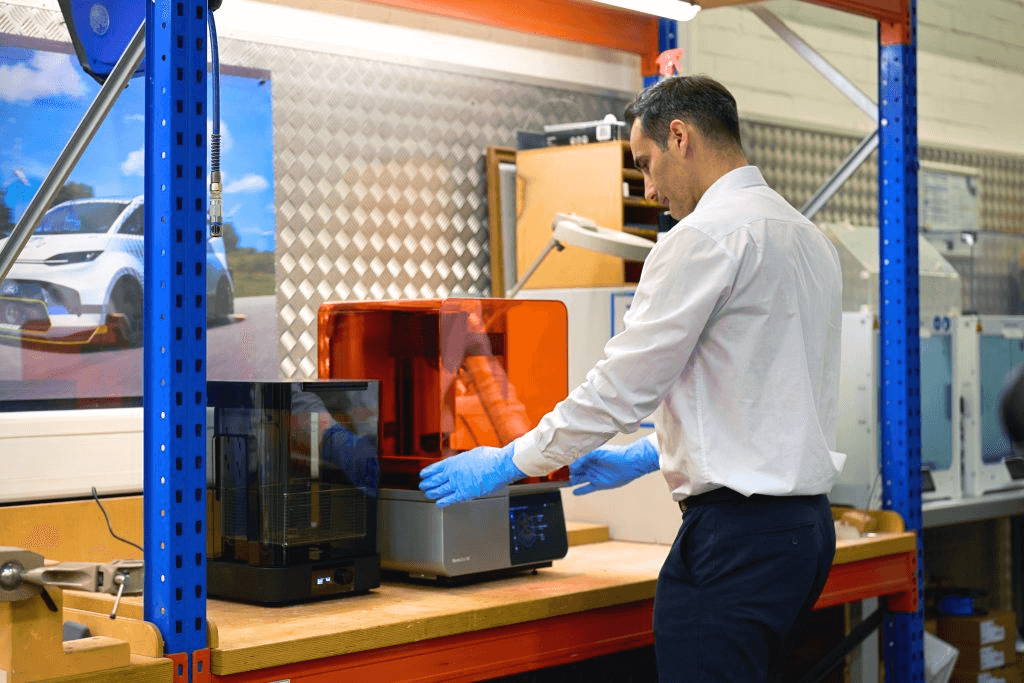
( Снимка чрез Formlabs ).
„Form 4 е много бърз, мисля, че това е най-добрата машина, която съм виждал досега по отношение на скоростта. Това наистина е много добро подобрение в сравнение с предишните модели,” коментира Alves. „Работата е по-лесна, така че е много по-лесно за операторите в нашия сервиз да се научат как да работят с машината и да получават части с добро качество.“
Piroddi нарече Form 4 „променител на играта“ благодарение на бързите скорости на 3D печат, което позволява на екипа за разработка на Ford да увеличи производителността и да постигне повече гъвкавост на дизайна. Екипът вече може да изпълнява повече заявки за по-малко от 24 часа и да доставя пратки с части за една нощ до Обединеното кралство.
SLA 3D печатът изигра ключова роля при валидирането на дизайна на много външни и вътрешни части за новия Ford Electric Explorer. Form 3L на Formlabs, широкоформатен SLA 3D принтер, беше използван за 3D отпечатване на големи външни части в едно цяло. Това включва капачката на огледалото за обратно виждане, капака на порта за зареждане и функциите на таблото.
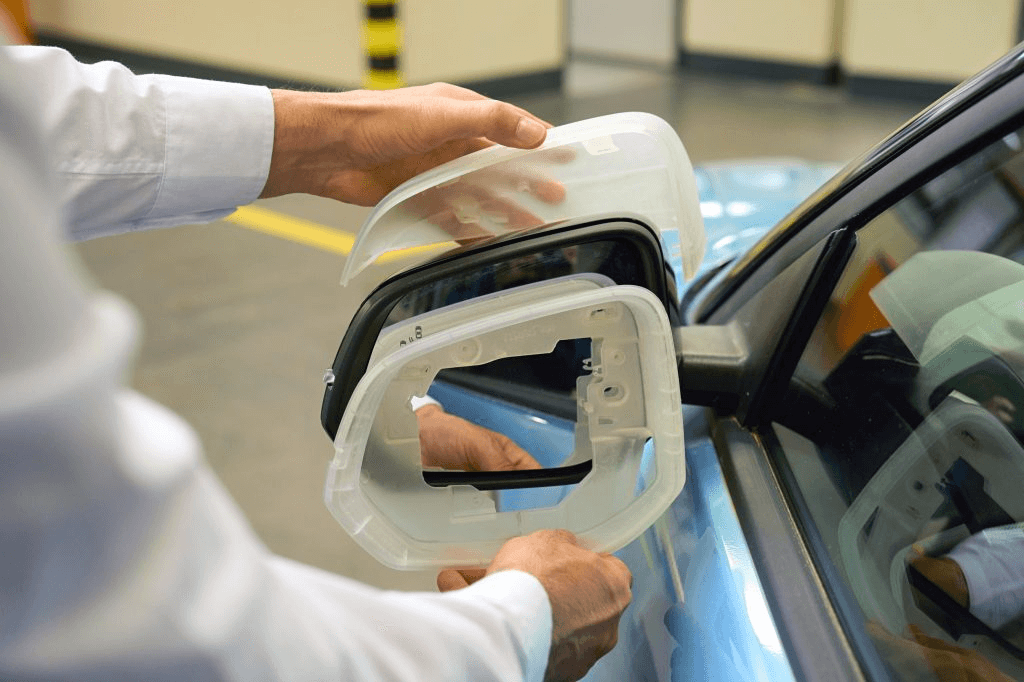
3D отпечатан прототип на огледало за обратно виждане. ( Снимка чрез Formlabs ).
SLS 3D печатът рационализира прототипирането на електрически превозни средства
Ford също оперира с голям набор от SLS 3D принтери за тестване на механични автомобилни части, включително Fuse 1+ 30W на Formlabs, който може да 3D отпечатва PA-12 полиамиден материал. Това притежава свойства, които са много подобни на шприцованите части за масово производство.
Компанията беше и една от първите, които бета тестваха автоматизираната система за почистване и полиране Fuse Blast на Formlabs. Твърди се, че това е ускорило процеса на създаване на прототипи на Ford, като е премахнало необходимостта от ръчна последваща обработка.
Ключово предимство на SLS технологията е, че тя не изисква поддържащи структури, което й позволява да отпечатва 3D по-сложни дизайни. Като такъв, Fuse 1+ 30W е използван за производството на различни механични части и възли за новия Explorer. Това включваше сложния порт за зареждане на електрическия SUV, който според съобщенията не би могъл да бъде прототипиран с друг метод на производство.
„Това е наистина сложен дизайн, който не можем да произведем по друг начин. Не можем да фрезоваме тази част. Не можем да използваме леене под налягане, за да произведем само някои проби“, каза Alves. „Така че най-добрият начин е да отпечатаме в материал, който можем да тестваме физически.“
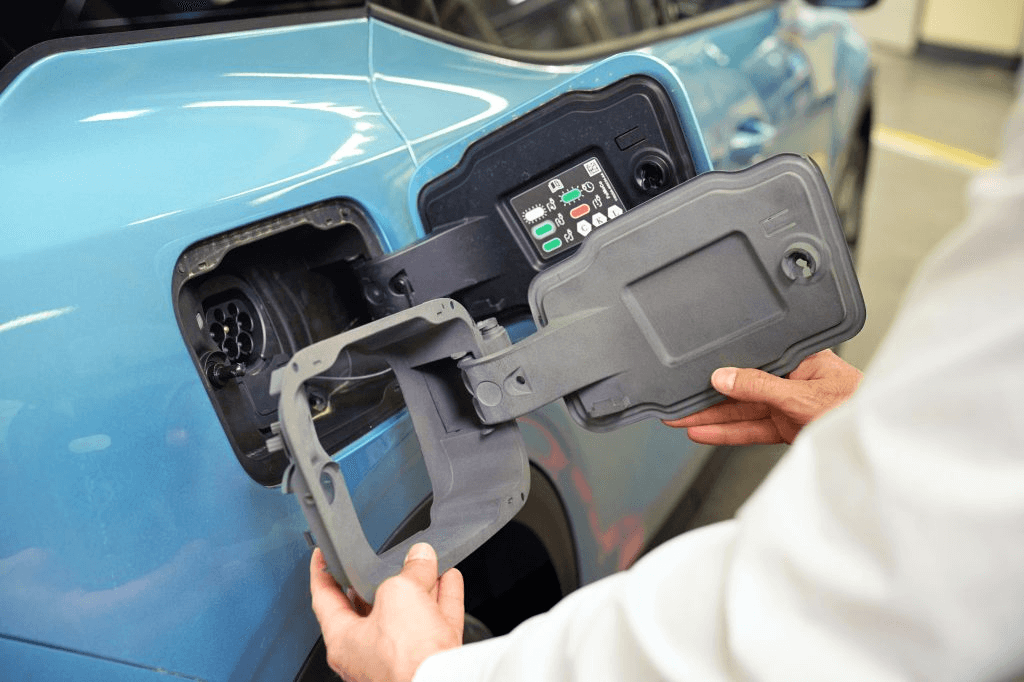
Прототип на порт за зареждане, 3D отпечатан върху Fuse 1 + 30W . ( Снимка чрез Formlabs ).
3D принтирането отключва вътрешното леене под налягане
Ford също така комбинира традиционните производствени процеси с 3D отпечатани бързи инструменти. Това позволява на екипа да определи и избере най-подходящия производствен процес и материал за различни приложения, намалявайки разходите и повишавайки ефективността на работния процес.
При краш тестове на превозни средства компонентите трябва да бъдат изработени от същия материал и процес като масово произвежданата крайна част. Пластмасовите части обикновено се произвеждат чрез леене под налягане, което обикновено изисква скъпи и отнемащи време метални инструменти.
„Виждаме голям потенциал при използването на вложки за 3D печат за леене под налягане въз основа на факта, че можем да повтаряме дизайна много бързо. Отпечатваме кухини в сърцевините и след това можем да ги променим в инструмента и да инжектираме частите“, добави Alves.
За новия Explorer, Ford произвежда гумени компоненти за сглобяването на дръжката на вратата на SUV собствено производство, използвайки 3D отпечатани вложки за матрица. Външното леене под налягане обикновено отнема два до три месеца. Въпреки това, чрез допълнително производство на вложките вътрешно произ, Ford може да завърши този процес за по-малко от три седмици. Екипът отпечата 3D вложките на формата в твърда 10K смола на техните SLA 3D принтери и найлон 12 прах на SLS.
„За този проект, ако трябваше да използваме външни инструменти, щеше да отнеме много повече време и нямаше да можем да доставим частите навреме“, обясни Alves.
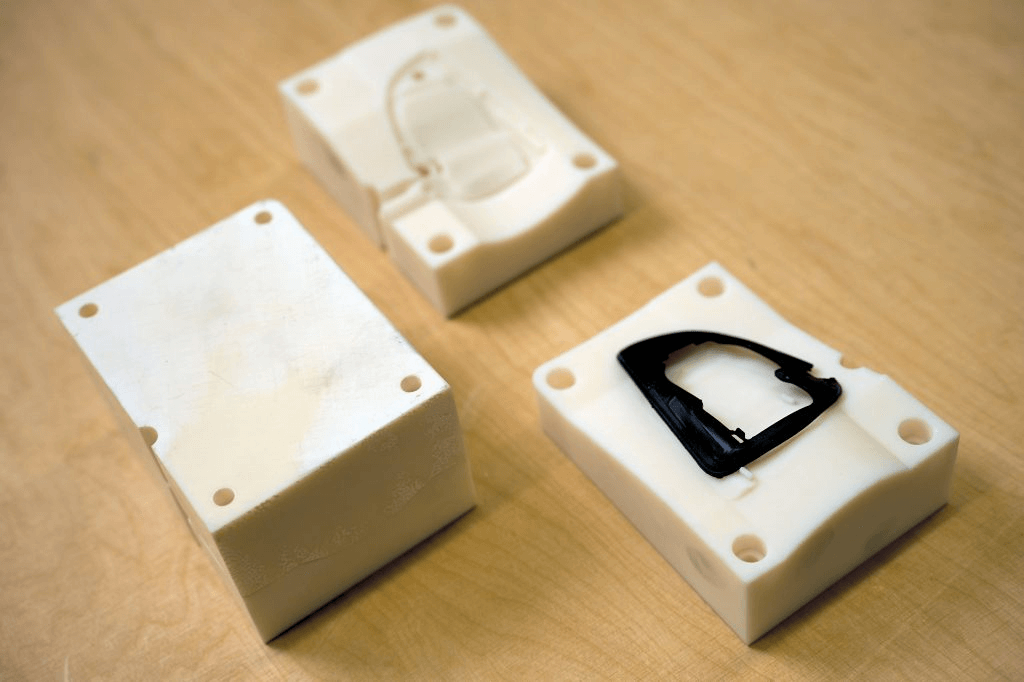
Вложки за леене под налягане, 3D отпечатани в Formlabs Rigid 10K Resin. ( Снимка чрез Formlabs ).
Производство на добавки за автомобилни приложения
Ford не е единственият производител на автомобили, който интегрира адитивното производство в своя работен процес по проектиране и производство.
Миналата година глобалният промишлен производител на 3D принтери INTAMSYS си партнира с доставчика на печатни материали KEXCELLED, за да предостави възможности за FDM 3D печат на автомобилния отдел на SIKA в Китай.
Чрез 3D отпечатване на автомобилни части , SIKA е спестила време и разходи до 90% за своите автомобилни прототипи и етапи на развитие. Технологията за 3D печат на INTAMSYS също е използвана за производството на интериорни и екстериорни автомобилни аксесоари, включително персонализирани брони, пробни части на волана, части за състезателни автомобили и елементи за лого на задната част.
На други места японската автомобилна мултинационална компания Toyota вече е използвала Zortrax M300 Plus за 3D печат на монтажни приспособления. Съобщава се, че приемането на FDM 3D принтера е оптимизирало операциите по сглобяване на превозни средства, намалявайки разходите и времето за изпълнение зад производството на основни инструменти и резервни части.
Специализираните лаборатории на Toyota за 3D печат, базирани в тяхното съоръжение в Полша, са инсталирали оборудване Zortrax на стойност повече от 100 000 злоти ($23 000). Частите, които в момента се отпечатват 3D в завода, попадат в четири категории: позициониращи приспособления, приспособления за сглобяване, инструменти за сглобяване и капаци. Тези части често се комбинират с други компоненти, произведени чрез субтрактивни процеси, за да образуват интегрирани възли.
Ние, от 3MG Bonev Ltd., като фирма партньор на Formlabs и INTAMSYS , можем да Ви предложим продажба, обучение, гаранционна и извън гаранционна поддръжка и обслужваne. Материали, консумативи и резервни части може да закупите от нас. Не се колебайте да отправите запитване към нас. Може да използвате различните възможности за свързване с нас:
https://3dservices.cloudcart.net/contacts
https://3dservices.cloudcart.net/category/3d-printeri-formlabs